How does the manufacturing process of plastic aprons differ from other types of aprons
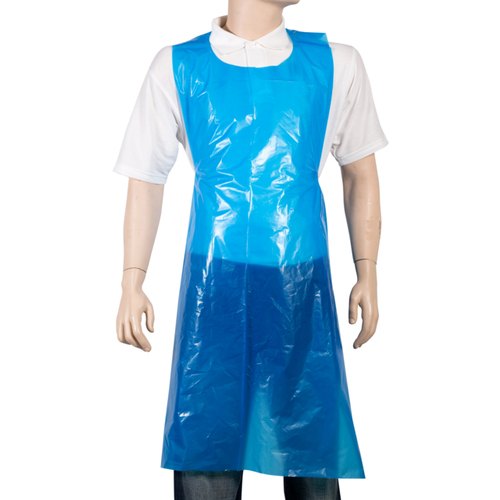
The manufacturing process of plastic aprons differs significantly from that of other types of aprons, primarily due to the materials used and the production techniques involved.
Plastic aprons are typically made from lightweight plastic materials such as polyethylene (PE) or polyvinyl chloride (PVC), chosen for their water resistance, dirt resistance, and ease of cleaning. The process begins with the creation of plastic polymers, usually through the polymerization of monomers derived from natural gas or crude oil. These polymers are formed into pellets, which are then melted and extruded into thin plastic sheets using specialized dies. The sheets are cooled rapidly to maintain their shape, and then automated cutting tools shape them into aprons. The edges are heat-sealed to prevent tearing and ensure durability. The entire process is highly automated and optimized for large-scale, high-speed production, with rigorous quality control checks at each stage.
In contrast, other types of aprons—such as those made from cotton, polyester, or blended textiles—undergo a more traditional textile manufacturing process. This typically involves spinning fibers into yarn, weaving or knitting the fabric, dyeing, cutting, and sewing the material into the final apron shape. Textile aprons may also require additional treatments for stain resistance or waterproofing, and the process is generally more labor-intensive and less automated compared to plastic apron production.
In summary, plastic apron manufacturing is characterized by the use of synthetic polymers, extrusion, heat sealing, and high-volume automation, while fabric apron production relies on conventional textile techniques and manual assembly. These differences result in plastic aprons being more suitable for disposable, high-hygiene applications, while fabric aprons are favored for durability and comfort in repeated use.
Conclusion
In conclusion, the manufacturing process of plastic aprons stands apart from that of traditional fabric aprons due to its reliance on synthetic polymers, highly automated production, and specialized finishing techniques. Plastic aprons are typically produced from materials such as polyethylene, which undergoes polymerization, pelletization, and extrusion into thin films. These films are then precision-cut and heat-sealed to form the final apron shape, ensuring uniformity, water resistance, and durability—qualities that are essential for environments demanding hygiene and protection. The speed and efficiency of this process allow for mass production, making plastic aprons an affordable and practical choice for disposable use in healthcare, food service, and industrial settings.
In contrast, fabric aprons are created through a more labor-intensive process involving spinning, weaving or knitting, dyeing, cutting, and sewing. Some fabric aprons are further enhanced with plastic coatings or laminates to improve their protective qualities, but these still require manual assembly and finishing steps. The result is a product that emphasizes comfort and reusability over disposability and cost-effectiveness.
This distinction in manufacturing processes highlights why plastic aprons are favored for single-use applications, while fabric aprons remain the standard for long-term, repeated use. The ability of plastic apron manufacturers in India to leverage advanced machinery and automation has positioned them as key suppliers and exporters in the global market, meeting the growing demand for hygienic, disposable protective wear. Plastic apron suppliers in India and plastic apron exporters in India continue to innovate, ensuring that their products adhere to international standards of quality, safety, and efficiency.
Ultimately, understanding these differences enables buyers to make informed decisions based on their specific requirements—whether prioritizing hygiene, cost, durability, or environmental considerations. The evolution of manufacturing techniques ensures that both plastic and fabric aprons serve their unique roles effectively across diverse industries.